Lo Studio dei Tempi e Metodi
A dimostrazione di quanto sia importante l’attività di Analisi Tempi e Metodi per Leanpull, abbiamo creato una tabella di valutazione per giudicare quale livello di competenza (Assessment) si è raggiunto nel ruolo di Analista Tempi e Metodi, questa utile scorecard di valutazione aiuta le aziende a gestire il livello di competenza di questa importante professione e definire quali passi debbano essere fatti per avere in azienda un vero Esperto di Analisi Tempi e Metodi.
Questa scheda considera non solo le competenze di un Analista Tempi e Metodi ma anche la capacità di utilizzo dei diversi sistemi di rilevazione (cronometrica, MTM, work sampling,..)
La scheda permette di valutare la professionalità raggiunta dandone un punteggio, il livello 1 indica una competenza limitata, il livello 5 indica il livello di Eccellenza, raggiungere tale livello considera una completa conoscenza delle applicazioni dell’Analisi Tempi e Metodi nonché aspetti legati al Miglioramento Continuo, Lean e Standard Work.
SCOPO DI UN ESPERTO DI TEMPI E METODI
Veniamo adesso a definire in dettaglio le basi dei Tempi e Metodi partendo da quale sia lo scopo principale di un’analisi Tempi e Metodi.
Andiamo per ordine, cominciamo a distinguere tra Analisi dei Tempi ed Analisi dei Metodi.
Partiamo dall’elencare tutti gli scopi di una Rilevazione dei Tempi di lavoro.
Analisi dei Tempi
Lo scopo principale di una Analisi dei Tempi è quella di conoscere in modo preciso la durata di una operazione, di una attività, one permetterne poi il controllo, la valutazione, la gestione.
Nel dettaglio:
- Stabilire la durata delle fasi
Un qualsiasi studio necessita di parametri di misura per determinare le fasi operative che costituiscono un ciclo di lavoro, questi parametri sono i Tempi di lavoro (vale per qualsiasi tipologia di attività, produttiva, amministrativa, ecc..)
- Migliorare l’utilizzo di macchine ed impianti
Conoscenza dei tempi macchina e dei tempi di intervento permette di determinare i cicli macchina meglio rispondenti alle esigenze produttive.
- Programmare il lavoro
La conoscenza dei tempi è fondamentale per lo svolgimento della programmazione del lavoro, per prevedere in modo preciso la migliore sequenza delle operazioni e per ottimizzare il flusso del materiale attraverso un carico costante (Flusso importante anche nell’applicazione della Lean Manufacturing)
- Metodi alternativi
La conoscenza dei tempi permette di poter scegliere fra due o più metodi quale sia il migliore in funzione dell’obiettivo da raggiungere.
- Determinazione dei costi standard
Lo studio dei Tempi è fondamentale per una buona determinazione degli standards di lavoro e base di partenza per la determinazione dei conseguenti costi standard
- Introduzione sistemi di incentivo
Per la determinazione di un sistema di incentivo richiede la conoscenza sufficientemente esatta della durata di ciascuna operazione a rendimento normale (vedi scale di rendimento) di una persona di normale capacità, ciò può essere ricavato solo attraverso lo studio dei Tempi.
- Calcolo della produzione
Lo Studio dei Tempi serve per valutare il contenuto di lavoro per ogni operazione e quindi a definire un livello di produzione accettabile per l’azienda.
- Calcolo risorse, uomini, macchine, necessarie per un determinato volume produttivo
Ogni prodotto è costituito da più parti, da un determinato ordine, con un suo particolare ciclo, costituito da una sequenza di operazioni.
Conoscendo il tempo di ogni operazione è possibile calcolare l’impegno a fronte di un programma di produzione e determinare i fabbisogni sia di risorse umane che di attrezzature ed impianti.
Passiamo ora alla parte di Analisi dei Metodi.
Lo scopo di una Analisi dei Metodi è l’analisi ed esame critico dei sistemi esistenti o previsti per compiere una determinata attività e nello sviluppo di un Metodo Migliorato, più efficiente, per compiere un determinato lavoro.
Con l’Analisi dei Metodi si pongono le premesse per capire come razionalizzare l’impiego delle risorse e dei materiali, mentre con lo studio dei Tempi si ottengono i dati che permettono di valorizzare il risparmio ottenuto con un nuovo metodo.
Gli obiettivi dello studio dei Metodi:
- Migliorare il processo e i procedimenti (eliminare i lavoro inutili, nel gergo Lean, le attività NVA non a valore) , semplificare il lavoro e standardizzarlo
- Migliorare il layout dell’area di lavoro e delle postazioni di lavoro (ottimizzazione dei flussi e della movimentazione, miglioramento dell’ergonomia)
- Perfezionamento degli impianti e delle attrezzature
- Miglior impiego dei materiali, degli impianti e delle risorse umane
- Migliorare l’ambiente di lavoro
- Riduzione dello sforzo e della fatica
Riassunto Procedura standard di ANALISI TEMPI E METODI
Per fare una Analisi dei Tempi:
- Selezionare l’operazione da rilevare
- Definire il metodo ideale da rilevare
- Raccogliere informazioni
- Dividere l’operazione in elementi
- Eseguire la rilevazione (scelta del metodo di rilevazione)
- Applicazione dei tempi
- Standardizzazione dei Tempi.
Per uno Studio dei Metodi:
- Scelta del lavoro da studiare
- Definizione degli obiettivi da raggiungere
- Analisi dei fatti e raccolta informazioni
- Esame critico dei fatti
- Sviluppo del nuovo metodo
- Definizione del nuovo metodo
- Implementazione e simulazione del nuovo metodo
- Correzioni
- Mantenimento e controllo del metodo applicato
Contattaci per avere maggiori informazioni su come avere in azienda un Esperto di Analisi Tempi e Metodi.
Nel nostro team abbiamo tra i maggiori professionisti italiani nello studio dei Tempi e Metodi, oltre 30 anni di attività sul campo (formazione Pirelli), siamo in grado di svolgere progetti di ottimizzazione processi per settori diversificati (metalmeccanico, automotive, abbigliamento, logistica, food, chimica, retail, office), possiamo inoltre definire un percorso formativo di Specializzazione di Analisti Tempi e Metodi, introducendo concetti e linee guida di Lean Manufacturing e Standard Work.
Segreteria@leanpull.com
Stefano.lecchi@leanpull.com
mobile +39 338 36 22 206
Spesso nelle attività di consulenza, nei progetti di miglioramento mi viene fatta la seguente domanda:
Ma come faccio a sapere se stò applicando veramente una metodologia Lean?
A questa domanda rispondo sempre allo stesso modo dicendo:
Provate ad andare in un processo, un’area produttiva, un ufficio, durante un giorno di festività, in cui non è presente nessuno.
Bene, fatevi un giro cercando di capire quali informazioni sono evidenti, capire quali sono le attività che vengono svolte, come vengono risolti i problemi, capire come si pianificano i compiti, che risultati stanno ottenendo, come vengono gestiti gli archivi, le attrezzature, …..
Più informazioni riuscite a carpire più significa che le buone pratiche Lean si stanno implementando nel modo corretto.
Al contrario, se nel visitare un’area fate fatica ad interpretare ed avere informazioni riguardo cosa facciano lì, allora la strada verso il miglioramento Lean è ancora lontana.
Una delle metodologie di miglioramento Lean più applicate dal team Leanpull riguarda lo SMED (Single Minute Exchange of Die), utile per la riduzione dei Tempi di Attrezzaggio e Set Up di un impianto.
Gli effetti positivi di un progetto SMED si riflettono su molteplici aspetti, riduzione dei tempi persi e di preparazione, riduzione del lead time, riduzione delle scorte, possibilità di produrre lotti più piccoli, aumento della flessibilità di un processo, riduzione delle attività NVA a non valore aggiunto, meno scorte, incremento dell’Efficienza Impianti O.E.E., ma non solo, la metodologia è fondamentale anche per catturare tutte le criticità e le debolezze di un impianto e di conseguenza introdurre azioni di miglioramento utili e renderlo più efficiente nel tempo.
- I vostri reparti misurano i Tempi di Set Up?
- Gli indicatori e i dati quotidiani sull’andamento dei set up sono disponibili per essere analizzati?
- Vengono periodicamente intraprese azioni di miglioramento sui Set Up?
Sono numerosi oramai i progetti SMED che abbiamo completato con successo e che stiamo tutt’ora sviluppando, queste esperienze continue ci permettono di accrescere sempre più la nostra esperienza su questa importante metodologia applicata in svariati settori.
Abbiamo ottenuto notevoli risparmi economici e saving con i nostri progetti.
A dimostrazione della nostra esperienza nello sviluppo della metodologia riportiamo di seguito alcuni progetti applicati in altrettante realtà aziendali:
Azienda: CPM Bearings S.p.A.
Azienda: Lagor S.r.l.
Azienda: Modecor Italiana S.r.l.
Azienda: Bouvard Italia S.p.A.
Azienda: Lord Italia S.r.l.
Azienda: Industrie Saleri Italo S.p.A.
Azienda: Fae Technology S.p.A.
Azienda: Keyline S.p.A.
Azienda: Agco S.p.A.
Azienda: Bonomi Industries S.r.l.
Azienda: Deoflor S.p.A.
Azienda: Fincantieri infrastructure S.p.A.
Azienda: Oleificio Zucchi S.p.A.
Azienda: Oscartielle S.p.A.
Azienda: Comap Italia S.p.A.
Azienda: Prince S.p.A.
(Contataci per valutare insieme le tue esigenze)
Per avere il massimo risultato operativo nel team di progetto si consiglia di avere anche il personale di reparto coinvolto della riorganizzazione, questo dà modo di poter riprogettare le aree di lavoro garantendo il mantenimento stesso dei risultati ottenuti, aumentando motivazione, responsabilità e credibilità verso il resto dell’organizzazione .
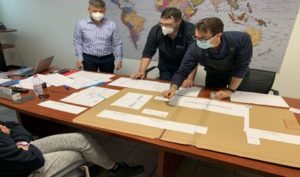
E’ un attività di team che permette di distribuire e disporre in modo ottimale macchinari , impianti, risorse e materiale.
Vale sia per contesti produttivi ma anche per aree logistiche ed uffici.
Non esistono soluzioni precostituite, ma vale la regola del miglior layout per la specifica esigenza, alcuni spunti:
- Semplificare flussi dei materiali
- Ridurre gli spostamenti degli operatori
- Aumentare la flessibilità del processo per garantire la gestione di variazioni di mercato.
(nella foto una Spaghetti chart per analisi dei flussi di una Operazione, Stato Attuale, si può notare come la movimentazione della persona addetta a svolgere l’attività sia completamente disorganizzata e dispersiva)
Solitamente un progetto di Re Layout parte da una esigenza specifica dell’azienda, alcuni esempi:
- Obsolescenza delle attrezzature
- Riprogettazione parziale o totale del prodotto
- Variazioni del volume di domanda
- Frequenti infortuni , necessità di maggiore ergonomia
- Necessità di riduzione dei costi
- Cambiamenti nel mercato
(nella foto una flow chart analisys per l’analisi delle attività, permette di identificare una serie di importanti dati come, attività a valore e attività no a valore, movimentazione, tempistiche, sbilanciamenti produttivi, ….)
A questo punto occorre rendere chiari e sintetici gli obiettivi da raggiungere, ecco degli esempi:
- Migliorare il livello di servizio: affidabilità, rapidità, flessibilità
- Aumentare Qualità della consegna: packaging, errori, rotture
- Ridurre i Costi
- Eliminazione degli sprechi : produzione in eccesso , scarti , rilavorazioni , attese , scorte , movimentazione, controlli
Quali sono gli attori coinvolti, chi dovrebbe far parte del team di progetto?
Come già detto in precedenza sicuramente gli attori principali di un Re layout dovrebbero essere le persone che quotidianamente agiscono e vivono nel contesto in cui sviluppare il progetto, questo per garantirsi sia una fonte inesauribile di informazioni sia per un buon mantenimento dei risultati ottenuti.
A completamento del team sarà necessario avere un Project Leader con capacità tecniche, organizzative e motivazionali, ed una serie di servizi a supporto del progetto:
– industrializzazione ( engineering )
– produzione
– logistica
– manutenzione
– pianificazione della produzione
Abbiamo seguito diversi progetti di Re layout aziendale, ottenendo notevoli risultati di miglioramento.
Se sei interessato ad approfondire l’argomento contattaci, saremo lieti di poter analizzare le tue esigenze e poter definire un progetto di miglioramento condiviso.
Stefano Lecchi
segreteria@leanpull.com
stefano.lecchi@leanpull.com
mobile 338 36 22 206
Kaizen, una parola molto usata quando si parla di miglioramento dei processi, forse a volte male interpretata ….
Facciamo un po’ di chiarezza su questo importante parola.
Partiamo dal tradurre questa parola giapponese
Kai = Nuova Sfida e Zen=Mente e Spirito
Già il significato ci aiuta a capire quando sia profondo il suo significato, ma vorrei riassumere tutto ciò con un concetto più ampio:
KAZIEN = PICCOLI CAMBIAMENTI INCREMENTALI CHE DIVENTANO UN CAMBIAMENTO FILOSOFICO, UN CAMBIAMENTO DI ABITUDINI.
Fare Kaizen significa imparare a fare le cose quotidiane in un modo diverso, tutti i giorni.
Nel fare Kaizen vi sono aspetti metodologici ma anche tecniche di coaching e coinvolgimento, tutto quello che può essere utile a cambiare le nostre abitudini, specie tutti quegli aspetti della nostra vita lavorativa quotidiana che riteniamo “normale” ma che invece è fonte di inefficienze, perdite di tempo e di conseguenza demotivazione.
Il Kaizen Event (Evento Kaizen)
Gli eventi Kaizen sono iniziative mirate, che solitamente possono essere condotti per realizzare miglioramenti in aree specifiche e per aiutare a convertire la cultura nel cambiamento quotidiano.
I Kaizen Event sono utili per dare un forte impulso, un segnale di cambiamento distintivo.
I Kaizen Event possono essere classificati in diverse tipologie:
Kaizen Projects, svolti con una frequenza di una o due volte a settimana fino al completamento del progetto di miglioramento, gli incontri possono durare dalle 1 o 2 ore a giornate intere.
Kaizen Blitz, sono eventi di miglioramenti singoli che possono avere durate differenti, mezza giornata, un girono, ….
Le tipiche attività che vengono svolte in un Evento Kaizen possono essere:
Ridurre i tempi di Set Up
Implementare una cella di lavoro
Implementare un sistema di Manutenzione Preventiva
Condurre un evento 5S
Definire un sistema a Kanban
….
Il Kaikaku
Altra terminologia dal significato importante, Kaikaku = Rivoluzione
Si traduce in una visione che il team impegnato a fare miglioramenti deve avere, definisce quali siano le regole affinché’ il Lean sia catalizzatore per il cambiamento culturale e della leadership in un’azienda.
La visione si traduce nelle seguenti 10 regole del Kaikaku:
- Elimina il concetto tradizionale di metodi di produzione
- Pensa a come funzionerà il nuovo metodo, non a come non funzionerà
- Non accettare scuse. Negare totalmente lo status quo.
- Non cercare la perfezione. Un tasso di implementazione del 50% va bene fintanto che è fatto sul posto.
- Correggi gli errori nel momento in cui vengono trovati
- Non spendere soldi
- I problemi ti danno la possibilità di usare il tuo cervello
- Chiedi “perché” cinque volte
- Le idee di dieci persone sono meglio della conoscenza di una persona
- Kaikaku non conosce limiti
Il team Leanpull nel 2020 ha avuto l’opportunità di iniziare un’importante progetto di miglioramento per una storica azienda nazionale.
Leader assoluta nel settore navale, dai suoi cantieri nascono prodotti esclusivi, ammirati in ogni parte del globo.
Il progetto molto ambizioso ha avuto come scopo implementare una prima parte di Lean Trasformation, per un nuovo plant del gruppo, dedicato alla Cantieristica Civile.
La società progetta e realizza strutture in acciaio di grande dimensione, ponti e progetti industriali.
Il progetto ha visto un primo sviluppo di metodologie di Miglioramento Continuo e Lean Thinking nei processi produttivi del plant.
Sono stati definiti alcuni indicatori KPI di progetto per poter monitorare il miglioramento dei parametri produttivi.
Il buon livello di coinvolgimento del management e del team a permesso di raggiungere risultati significativi di incremento delle performance sulle aree in cui è stato promosso l’evento.
Il buon esito di questo primo progetto pilota ha permesso di poter proseguire questa prestigiosa collaborazione per tutto l’anno 2021.
In base alle competenze interne di un’azienda per mappare un processo dopo i primi 2 livelli base che abbiamo già visto c’è un terzo livello, questa si chiama Value Stream Mapping di Espansione, le classiche attività di Spegnere il Fuoco, comuni in organizzazioni poco efficienti dove le attività impreviste sovrastano quelle periodiche e pianificate, in questo caso sono ridotte drasticamente, la leadership dell’organizzazione interna verifica periodicamente e regolarmente lo sviluppo del Miglioramento Continuo, si adottano metodologie di Feedback Costruttivo. Il ruolo del Value Stream Manager è riconosciuto da tutti, l’A3 Practic Problem Solving è utilizzato per affrontare le cause e apportare miglioramenti, i problemi tendono a non ripetersi nel tempo.
Stefano Lecchi
Cookie e Privacy Policy
Lean Trasformation
Consulenza Lean Manufacturing, Lean Production, Lean Office. Applicazione metodologie WCM, Operational Excellence, Lean Start Up.
Lean Assessment, workshop 5S, Kaizen, Analisi Tempi e Metodi.
Industria 4.0: definizione road map per poter evolvere in una Smart Enterprise, ottenimento delle informazioni necessarie per cogliere le agevolazioni legate al Decreto Industria 4.0.
Servizi
Ultimi Articoli
- Assenteismo e turnover? Risolvili con il modello di coinvolgimento lean
- Come integrare Lean Thinking e Intelligenza Artificiale per il futuro dei processi
- Le resistenze al cambiamento: un ostacolo naturale ma prevedibile
- Operational Excellence: la chiave per aumentare produttività e coinvolgimento
- Cinque errori comuni che ostacolano il miglioramento continuo nelle PMI