L’intelligenza artificiale (AI) si basa su algoritmi e modelli matematici complessi progettati per emulare alcune delle capacità umane.
L’AI richiede una elevata quantità di dati per apprendere e migliorarsi nel tempo.
I dati possono essere strutturati (come database) o non strutturati (come testo, immagini, ….). La qualità e la quantità dei dati influenzano significativamente le prestazioni di un sistema di intelligenza artificiale.
I dati raccolti richiedono una fase di pre-elaborazione per renderli adatti all’uso nell’addestramento di modelli di intelligenza artificiale.
L’apprendimento automatico è una componente chiave dell’AI.
Gli algoritmi di apprendimento automatico consentono ai sistemi di analizzare i dati, identificare pattern e apprendere.
Gli algoritmi di apprendimento automatico vengono utilizzati per creare modelli che possono fare predizioni o prendere decisioni basate sui dati di input.
Una volta che il modello è stato addestrato e ottimizzato con successo, può essere implementato in un’applicazione o un sistema per svolgere attività specifiche, come il riconoscimento di immagini, la traduzione automatica, o il supporto decisionale.
Perché Lean e Intelligenza Artificiale?
Il Futuro dell’Ottimizzazione dei Processi passa attraverso un salto evolutivo in cui le metodologie di Miglioramento Continuo Lean hanno come potente alleato L’Intelligenza Artificiale.
L’Intelligenza Artificiale (AI) sta’ emergendo come un potente strumento in grado, attraverso una prima fase di Assessment e analisi dei processi, di creare sistemi di controllo e gestione che vanno a massimizzare i saving di miglioramento.
L’AI sta reinventando l’ottimizzazione dei processi, portando la Lean a nuovi orizzonti, mai visti in passato.
Si parla di Eccellenza Operativa Digitale dei processi (Digital Operational Excellence)
L’AI offre strumenti avanzati per analizzare grandi quantità di dati, identificare inefficienze e suggerire miglioramenti.
Questo si traduce in una maggiore reattività ed efficienza e nella capacità di prendere decisioni basate sui dati più rapidamente.
Possiamo prevedere trend futuri anticipando problematiche attraverso azioni correttive che eliminano sul nascere possibili pericoli.
I Casi di Successo nelle applicazioni della AI si moltiplicano.
Diverse organizzazioni stanno già sperimentando con successo diverse applicazioni, creando all’interno delle aziende nuove strategie e piani industriali di miglioramento, creando road map composte da metodologie Lean e modelli di AI.
Questi sono solo i primi casi che dimostrano quanto sia elevato il potenziale dell’AI nel mondo del Miglioramento Continuo.
In un Futuro Collaborativo L’AI non sostituisce l’elemento umano ma ne amplifica le capacità di gestione ed analisi, lasciando a quest’ultimo l’elemento base, la creazione del VALORE.
Insieme, possono creare un ambiente di lavoro più efficiente, innovativo e adattivo.
Alessandro Ruotolo fa’ parte del team Leanpull dedicato allo svilupp odi metodlogie e modelli AI.
Alessandro ha una vasta conoscenza del mondo Industria 4.0 relativamente all’integrazione software e macchinari di produzione, Digital Trasformation ed al Artificial Intelligence e la possibilità di seguire progetti di sviluppo software, dalla fase di requisiti a quella di delivery e training, e di migrazione infrastrutture IT in cloud.
Dal 2021 studia modelli di AI Artificial Intelligence e oltre che in Italia opera in Svizzera attraverso una sua start up, AI4FUTURE. www.ai4future.ch
E’ un prezioso supporto che, con la sua competenza e dedizione, ci permette di gestire al meglio progetti complessi di integrazione digitale e massimizzazione dei risultati..
Crediamo infatti che un team composto da esperti operativi di Lean ed Operational Excellence e professionisti abili nella creazione di modelli digitali dia il massimo dei benefici sia a breve termine che a medio lungo termine.
segreteria@leanpull.com
#intelligenzaartificiale #lean #operationalexcellence #smartmanufacturing #artificialintelligence #ai #leanpull #Stefanolecchi #alessandroruotolo
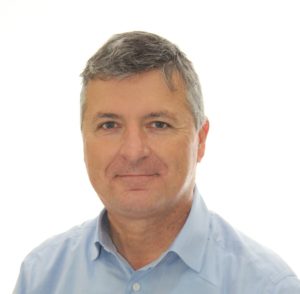
Contattaci per avere approfondimenti sull’argomento, i nostri esperti saranno lieti di presentarti le potenzialità di questi sistemi.
segreteria@leanpull.com